English
Technology
Intellectual Property Rights
Fuelsion Ltd has the Intellectual Property Rights over European, USA and Brazilian Patents Pending (WO 2021/090.010 A1, EP 4055127 A1, US 2022/370.965 A1, and BR 112022/008.209 A2), registered trademark N4NO® Tech (UK 00003.473.658), designs, and copyrights, currently assigned to the interim Chief Executive Officer (Serodio).
Invention
Patents Pending
In December 2013, Serodio invented the intellectual property that would lay the groundwork for his future innovations. By early 2014, he developed a formulation for producing WiDE (water in diesel nanoemulsions). In 2017, he created a novel method, system, and apparatus for producing onboard NEF (N4NO® Tech Environmental Fuels). This technology was designed to enhance combustion and thermal efficiency while simultaneously reducing implementation, operational, and fuel costs, as well as dependence on hydrocarbon fuels and exhaust gas emissions. On November 5, 2019, Serodio submitted a US Provisional Patent application to the USPTO (US Patent and Trademark Office) under the number US 62/931,084. He currently holds rights to pending patents in Europe, the USA, and Brazil, covering c.a. 60% of the global diesel market.
Brand Name
Registered Trademark
Serodio has registered the trademark N4NO® Tech, under no. UK 00003.473.658, on 9th of August 2020, in the IPO (Intellectual Property Office), United Kingdom, brand name used by Fuelsion Ltd to market NEF (N4NO® Tech environmental fuels) onboard technology.
Typical Application
HGV Trucks and Tractors
The primary target market is the road diesel freight transport segment, specifically targeting HGVs (Heavy Goods Vehicles), such as trucks and tractors. The NOPU (NEF Onboard Production Unit) [1] is installed in HGVs to produce NEF (N4NO tech Environmental Fuel). This fuel is temporarily stored in a 15-litre NEF "daily" tank [2]. The system aims to increase operational efficiency, improve mileage, and reduce both fuel and operational costs. By producing NEF onboard, the technology simultaneouly increases combustion efficiency, reduces the reliance on hydrocarbon fuels and significanlty lowers exhaust gas emissions.
Main Components
NEF Onboard Technology
The NOPU (box) [1] is designed with a lid (top) [1c] and includes two main inspection and maintenance doors: the LEME device door [1a] and the DI (deionised) filters door [1b]. The NOPU also comprises the NEB (NEF Emulsifying Blend) primary tank [4], NEB corrective tank [6], DI (deionised) filters [7], DI water tank [8], and connecting hoses [3], [5], and [9], along with the LEME (low-energy mixing and emulsifying) device [10]. Diesel is fed into the NOPU through the diesel inlet tube [A] using the system's flow energy. Filtered water is injected into the DI water filters [7] through water inlet tube [B]. Inside the NOPU, the diesel is processed in the LEME device [10], where the NEF (N4NO® Tech Environmental Fuel) is produced. The NEF is then sent to the NEF "daily" tank [2] via the outlet tube [C], ready for use in the vehicle.
HC Based Blends
NEF Emulsifying Blends
The NEBs (NEF Emulsifying Blends) are produced by mixing the Fn (formulation) with HC (hydrocarbon) at a ratio of c.a. 3:1. The Fn is designed to produced the smallest water sub-droplet particle size at operational temperatures. The hydrocarbon enhances the quality of the diesel, improving fuel efficiency and facilitating the flow of the formulation, which ultimately helps reduce operational costs. The primary NEB (NEF Emulsifying Blend) is poured into the NEB primary tanks [4], while the corrective NEB is added to the NEB corrective tank [6]. The NEB's are pre-mixed with the diesel in the LEM (Low Energy Mixing) chambers before being sent to mix with DI Water in the LEE (Low Energy Emulsifcation) chamber.
Nanoscaled Particles
DI (Deionised) Water
The key factors in producing the smallest water sub-droplet particle size are the selected surfactants and the temperatures for which the Fn has been designed. To ensure consistency and avoid potential engine damage, DI (deionised) water is produced for use onboard. Filtered water is sent through the water inlet port [B] to the cationic filter [7a], followed by the anionic filter [7b], before being stored in the DI water tank [8]. Cationic filters are typically used for the complete removal of hardness ions, while anionic filters are used for demineralization, dealkalization, and desilication, as well as for removing TOC (total organic carbon) or other organics. DI water is mixed with the pre-mixes (diesel & NEB's) in the LEE (Low Energy Emulsifcation) chamber, at variable water rates, to achieve the optimal NEF composition that matches the engine's operational conditions.
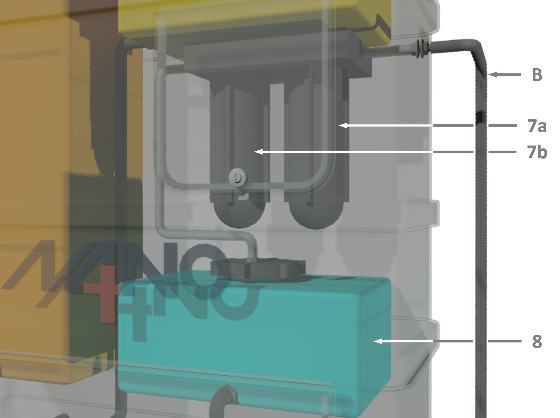
Production Method
Low Energy Mixing & Emulsying
NEF (N4NO® Tech Environmental Fuels) is produced onboard using the LEME (Low Energy Mixing & Emulsifying) device. The process begins as diesel is pumped through the diesel inlet tube [A] into the first mixing chamber [10aa], where it is blended with the primary NEB (NEF Emulsifying Blend) injected by the ACD (Automatically Controlled Dozer) [10ab] from the connecting hose [3]. The resulting pre-mix is then transferred to the second mixing chamber [10ba], where it is adjusted with corrective NEB, injected by another ACD [10bb] from the connecting hose [5], to account for any variations in the commercial diesel. Next, the pre-mix is directed into the emulsifying chamber [10ca], where it is combined with DI (Deionised) water injected by the ACD [10cb] from the connecting hose [9]. The final NEF is then transported through the NEF outlet tube [C] to the NEF "daily" tank, ready for use.
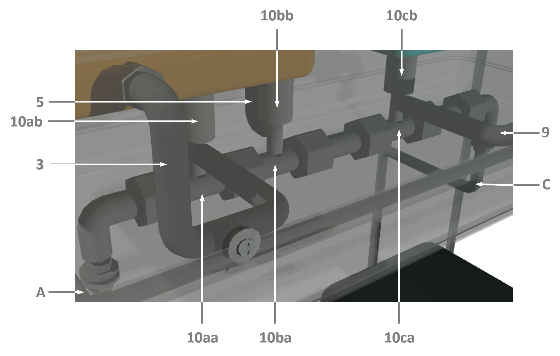
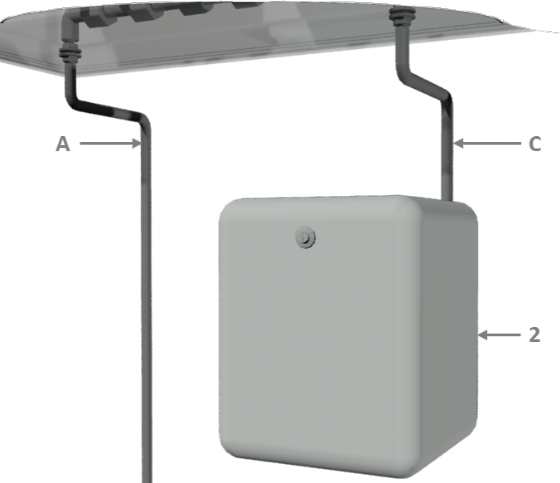
Environmental Fuel
NEF Tank (Low Volume)
Diesel is only used during the first two to three minutes when the engine starts from cold. After this, the NEF (N4NO® Tech Environmental Fuels) Onboard System activates, sending diesel to the NOPU (NEF Onboard Production Unit) through the diesel inlet tube [A] to produce NEF. The produced NEF is then sent through the NEF outlet tube [C] to the NEF "daily" tank [2]. During the initial two to three minutes, the NEF in the "daily" tank [2] recirculates and heats up before it is ready for use.
Data Management
NEF Intelligent System
The NIS (NEF Intelligent System) installed in the vehicle controls the production and quality of NEF (N4NO® Tech Environmental Fuels) based on the end-user's selected modes, such as prioritizing fuel cost savings or targeting specific emission reductions. The NIS adjusts the NEF parameters to match the engine's operational conditions, ensuring optimal performance. It also displays real-time information on the dashboard, including engine, vehicle, and NEF performance, while automatically transmitting this data to the franchisee and data management team for further analysis and support.
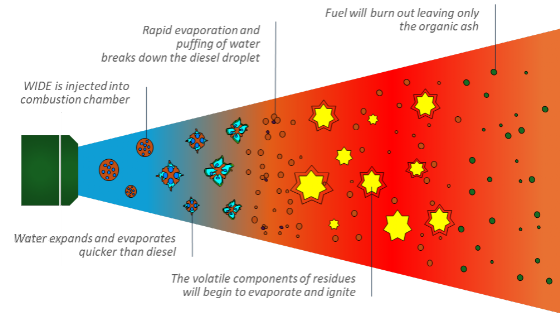
Thermal Efficiency
Microexplosion Phenomenon
When WiDE (water in diesel nanoemulsion) is injected into the combustion chamber, the water sub-droplets evaporate and expand more rapidly than diesel. This rapid evaporation and puffing cause the diesel droplet to break down into smaller parts, a process known as the microexplosion phenomenon. The volatile components of the remaining fuel then evaporate, ignite, and burn, leaving behind only organic residues. The nano-scaled water sub-droplet particles within the diesel droplets play a crucial role in enhancing combustion efficiency, thermal efficiency, and reducing exhaust gas emissions.
Evaporation/Puffing
Microexplosion Phenomenon
The evaporation ratio refers to the proportion of water sub-droplets that vaporize during the combustion process. Smaller water sub-droplets possess a higher surface area-to-volume ratio, which facilitates faster evaporation. Puffing forces are the forces exerted during the breakup of the diesel droplet into smaller droplets. Smaller water sub-droplets exert lower puffing forces, resulting in finer fuel spray droplets that can enhance combustion efficiency. By optimizing the particle size of water sub-droplets, combustion efficiency can be improved, leading to reduced emissions of CO (carbon monoxide) and UHC (unburnt hydrocarbons). Achieving the ideal balance between water sub-droplet size and puffing forces requires careful consideration of various factors, including the properties of NEF (N4NO® Environmental Fuel), injection parameters, and the design of the combustion chamber.
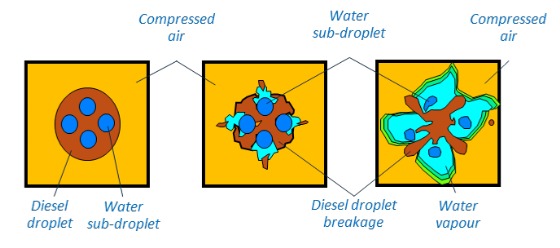